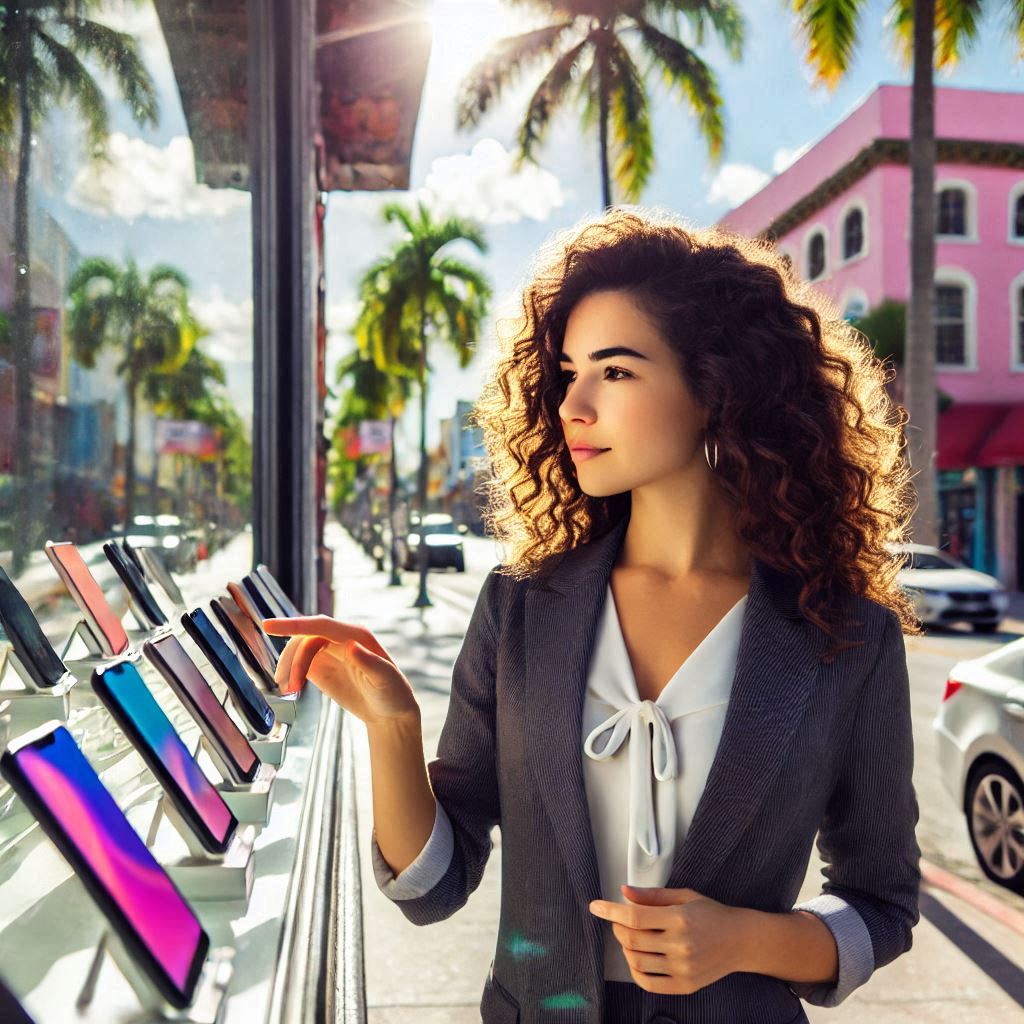
Okay, let’s break down the information provided by the Environmental Information Innovation Institute (EIC) regarding monthly inspections of local exhaust ventilation systems by Designated Chemical Substances and Organic Solvents Operation Supervisors, and expand on related information to make it easily understandable.
Core Information (Based on the EIC link provided):
The question, as gleaned from the translated title, addresses monthly inspections of local exhaust ventilation systems. The key takeaway is that a specifically trained and designated person – the “Designated Chemical Substances and Organic Solvents Operation Supervisor” – is responsible for performing these inspections.
Expanding on the Topic: Monthly Inspections of Local Exhaust Ventilation Systems
Let’s delve into the importance, process, and rationale behind these inspections.
1. What are Local Exhaust Ventilation Systems (LEV)?
- Definition: LEV systems are engineering controls designed to capture and remove hazardous air contaminants (fumes, dusts, gases, vapors) at their source, before they can spread into the general workplace air and be inhaled by workers. Think of it like a vacuum cleaner for industrial air.
- Components: A typical LEV system consists of:
- Hood: The point of capture. It needs to be properly designed and positioned to effectively capture the contaminants.
- Ductwork: Transports the contaminated air from the hood to the air cleaning device.
- Air Cleaner (Filter, Scrubber, etc.): Removes the contaminants from the air.
- Fan: Provides the airflow to move the contaminated air through the system.
- Exhaust Stack: Discharges the cleaned air to the outside atmosphere.
2. Why are Monthly Inspections Necessary?
- Worker Safety: The primary goal is to protect workers from exposure to hazardous chemicals and organic solvents. Inhaling these substances can lead to a range of health problems, from short-term irritation to long-term chronic diseases.
- Compliance with Regulations: Many countries and regions have regulations (like Japan’s Industrial Safety and Health Law) that mandate the use and maintenance of LEV systems when workers are exposed to hazardous chemicals. Regular inspections are a crucial part of demonstrating compliance.
- System Performance: Over time, LEV systems can degrade due to wear and tear, blockages, or improper use. Regular inspections help identify and correct problems before they compromise the system’s effectiveness.
- Preventing Accidents: A malfunctioning LEV system can lead to a buildup of flammable or explosive vapors, increasing the risk of fires or explosions.
- Environmental Protection: Some air cleaning devices remove hazardous materials to prevent them from being released into the environment.
3. Who is the “Designated Chemical Substances and Organic Solvents Operation Supervisor?”
- Role and Responsibilities: This individual has specific training and certification to oversee operations involving designated chemical substances and organic solvents. Their responsibilities include:
- Ensuring that LEV systems are properly designed, installed, and maintained.
- Conducting regular inspections.
- Supervising work practices to minimize worker exposure.
- Implementing emergency procedures in case of leaks or spills.
- Keeping accurate records of inspections and maintenance.
- Training and Certification: The requirements for becoming a supervisor vary depending on the jurisdiction, but typically involve completing a specialized training course and passing an examination.
- Legal Requirement: Having a designated supervisor is often a legal requirement when working with hazardous chemicals.
4. What Does a Monthly Inspection Involve?
The specific items to check will depend on the type of LEV system and the regulations in your area, but a typical monthly inspection includes:
- Visual Inspection:
- Hood: Check for damage, blockages, and proper positioning.
- Ductwork: Check for leaks, dents, and corrosion.
- Air Cleaner: Check for proper operation and maintenance (e.g., filter replacement).
- Fan: Check for unusual noises or vibrations.
- Exhaust Stack: Check for obstructions.
- Airflow Measurement:
- Use a manometer, anemometer, or other measuring device to verify that the system is providing adequate airflow at the hood. This is a critical step to ensure that contaminants are being effectively captured.
- Static Pressure Measurement:
- Measure the static pressure in the ductwork to identify any problems with airflow resistance.
- Filter Condition:
- Inspect air filters for dirt buildup and replace them as needed.
- System Controls:
- Verify that all system controls are functioning properly (e.g., fan switches, dampers).
- Documentation:
- Record all inspection findings, including any problems identified and corrective actions taken. This documentation is essential for demonstrating compliance and tracking the system’s performance over time.
5. Potential Issues and Corrective Actions:
During the inspection, look out for the following:
- Reduced Airflow: This could be caused by a clogged filter, a damaged fan, or obstructions in the ductwork. Corrective actions might include replacing the filter, repairing the fan, or removing the obstructions.
- Leaks in Ductwork: Seal any leaks to prevent contaminants from escaping.
- Damage to Hood: Repair or replace damaged hoods.
- Improper Hood Positioning: Adjust the hood to ensure that it is properly positioned to capture the contaminants.
- Excessive Noise or Vibration: This could indicate a problem with the fan or motor. Investigate and repair the problem.
6. Record Keeping:
- Importance: Accurate and complete records are essential for demonstrating compliance with regulations, tracking the system’s performance, and identifying potential problems.
- What to Record: Records should include:
- Date of inspection
- Name of inspector
- Inspection findings (including any problems identified)
- Corrective actions taken
- Airflow measurements
- Static pressure measurements
- Filter replacement dates
In summary:
Monthly inspections of local exhaust ventilation systems by qualified personnel (Designated Chemical Substances and Organic Solvents Operation Supervisors) are critical for protecting worker health, complying with regulations, and ensuring the effective performance of these vital safety systems. Proper training, thorough inspections, and diligent record-keeping are all essential components of a successful LEV program. Failure to maintain these systems can result in worker exposure, regulatory fines, and potential accidents. Always refer to local regulations and industry best practices for specific requirements.
The AI has delivered the news.
The following question was used to generate the response from Google Gemini:
At 2025-06-18 01:00, ‘特化物・有機溶剤作業主任者による局所排気装置の月次点検’ was published according to 環境イノベーション情報機構. Please write a detailed article with related information in an easy-to-understand manner. Please answer in English.
614